Green Iron and Steel Standards
The Green Hydrogen Organisation is working to improve green iron and steel standards. Clear standards and certification schemes are crucial for ensuring the sustainable and effective development of green iron and steel production and use, enabling informed decision-making, attracting investment, and fostering international trade.
Countries and companies are pulling global standards and certification schemes in different directions, depending on their hematite/magnetite exposure, access to scrap steel, and the outlook for incumbent/legacy and greenfield projects. Almost all of the existing standards and certification schemes in the iron and steel sector do not sufficiently prioritise net zero production pathways and thus risk lending credibility to iron and steel projects and products with unsustainable emissions. While there is broad based agreement that “a common understanding of existing and emerging definitions for near-zero emissions steel production is needed” (Steel Standards Principles, 2024) there is also a tendency to avoid setting specific thresholds that are clearly aligned with net zero commitments (nationally determined contributions).
In addition, most of the existing iron and steel industry standards focus exclusively on GHG emissions measurement and do not address wider sustainability considerations, including requirements on land use planning, water resource management, human rights, community benefits, transparency and consultation. Leveraging our experience with the green hydrogen standard, GH2 is working to strengthen global standards.
The Green Iron Opportunity
Green iron for a carbon-free steel sector
Steel is essential to modern infrastructure, but its production continues to be one of the most carbon-intensive industrial processes. Traditional methods rely heavily on coal-derived coke as both a fuel and reducing agent in blast furnaces. As a result, the steel industry emits 2.6 gigatons of CO2, accounting for about 7% of global emissions and surpassing the total emissions of the entire European Union.
Green iron offers a near zero carbon alternative. Instead of using coal, it is produced by reducing iron ore with green hydrogen through a process known as direct reduction. The hydrogen reacts with the ore to create “sponge iron” or direct reduced iron (DRI), which can be further processed into steel in an electric arc furnace. Unlike the conventional blast furnace route, this method emits only water vapour and can cut emissions by up to 97% when powered by renewable electricity and green hydrogen.
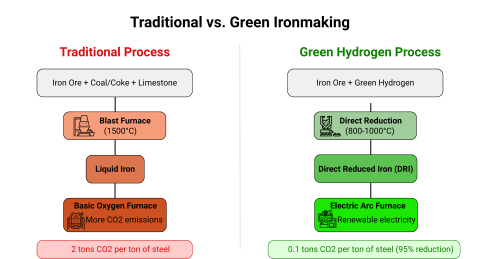
Green iron and industrial development
Several major projects are already pioneering green iron deployment, including HYBRIT and Stegra in Sweden, SALCOS in Germany, GravitHy in France, Boston Metal in the United States, Fortescue and NeoSmelt (in collaboration with BHP and Rio Tinto) in Australia. Near-zero-emissions steel production is technically viable and progressing rapidly in industrialised economies.
Few of these projects however focus on emerging and developing countries (EMDCs), where steel demand is expected to grow most rapidly. Without access to low-carbon technologies, these regions risk becoming locked into emissions-intensive production methods, delaying progress toward national development goals and global climate targets.
As a proven and scalable solution, green iron can enable sustainable industrial growth while supporting Sustainable Development Goals (SDGs,) such as SDG 9 (Industry, Innovation and Infrastructure) and SDG 13 (Climate Action). Expanding its reach to EMDCs is critical for an equitable and effective green industrial transition.